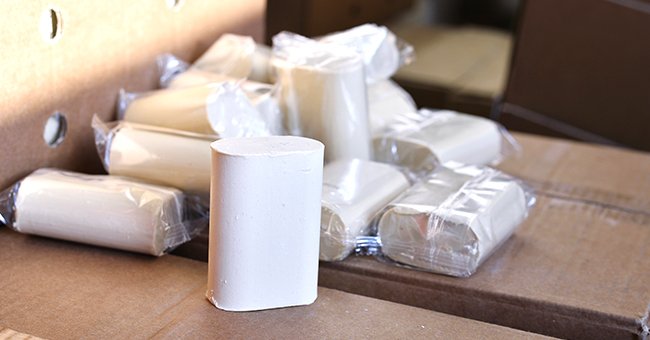
Daily Joke: Soap Factory Had Problems with Empty Boxes
A soap factory spent more than $10 million to overcome a defect in their manufacturing system, only for a junior team member to come up with a very cheap solution three weeks later.
Cleano soap ran into a production problem in their factory when buyers and distributors consistently complained that soapboxes were being sent out without any soap in them.
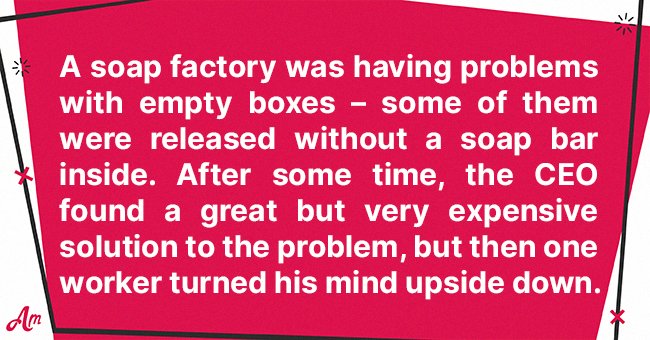
Source: Amomama
The Cleano CEO called in all of the top management which included three engineers so they could figure out a way to stop the defective orders from going out.
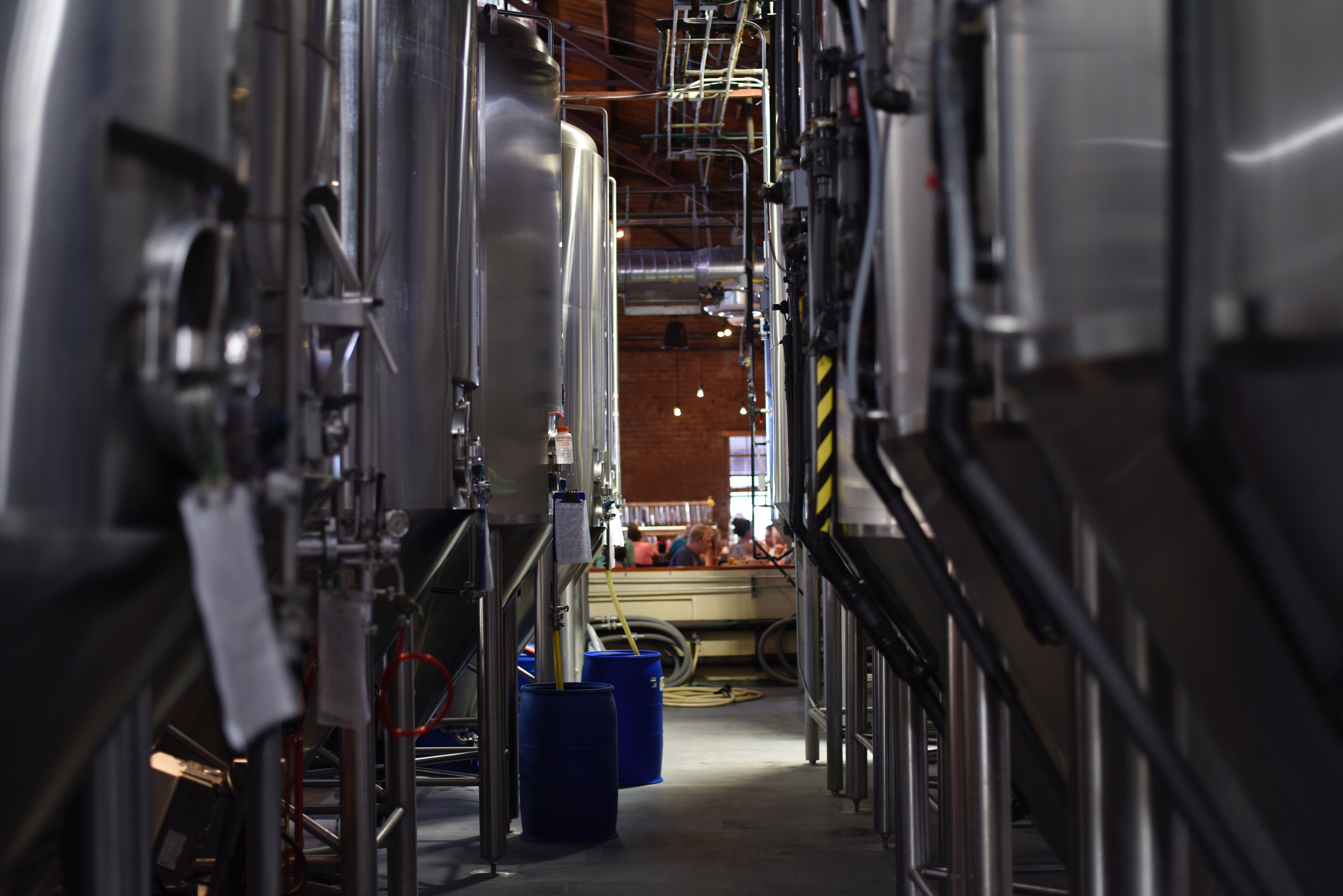
The inside of a factory. | Pexels/ ELEVATE
Three weeks later, the engineers came to the CEO with a brand new system they developed which was designed specifically for the soapbox problem.
They presented their solution and left the cost of their idea until the end. The CEO nearly choked on his coffee when he heard their design would cost $10 million to install and get up and running.
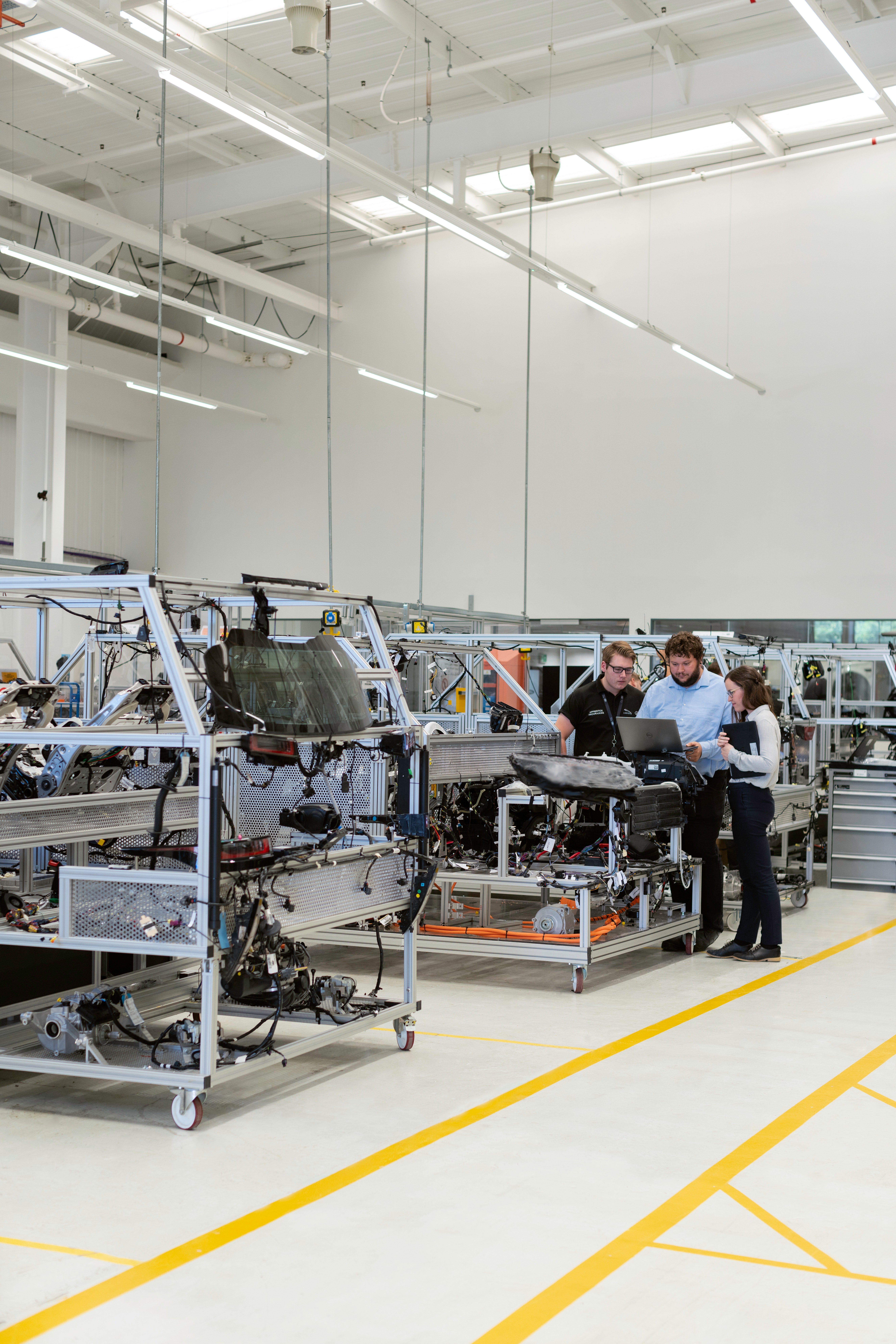
Three people conversing in a factory. | Pexels/ ThisIsEngineering
However, the CEO decided to bite the bullet and scraped together the money to have the design implemented. The engineers figured out that if they placed a scale toward the end of the production line, it would solve their problem.
The scale would then detect if the soapbox was too light, which means there is no soap in it, and a bell would go off, and the production line would halt so that someone could walk over and remove the empty box.
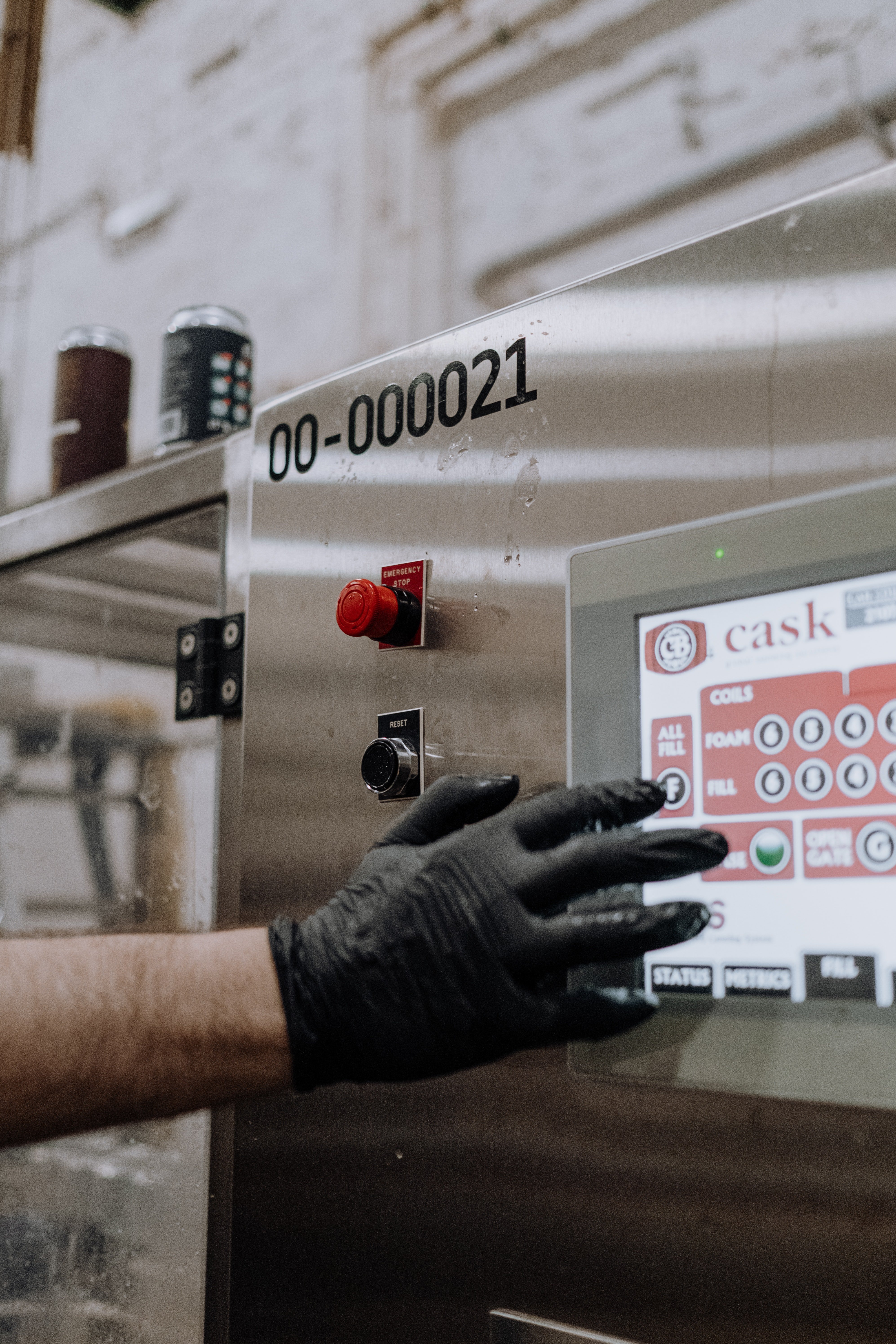
A person resetting a factory machine. | Pexels/ cottonbro
The first three weeks after the scale system was installed went by without a hitch. The buyers and distributors called in to say they weren't receiving any empty boxes, and they were happy.
The data showed all the empty boxes that were usually being sent out were being stopped and thrown out of the line before they were shipped to the distributors.
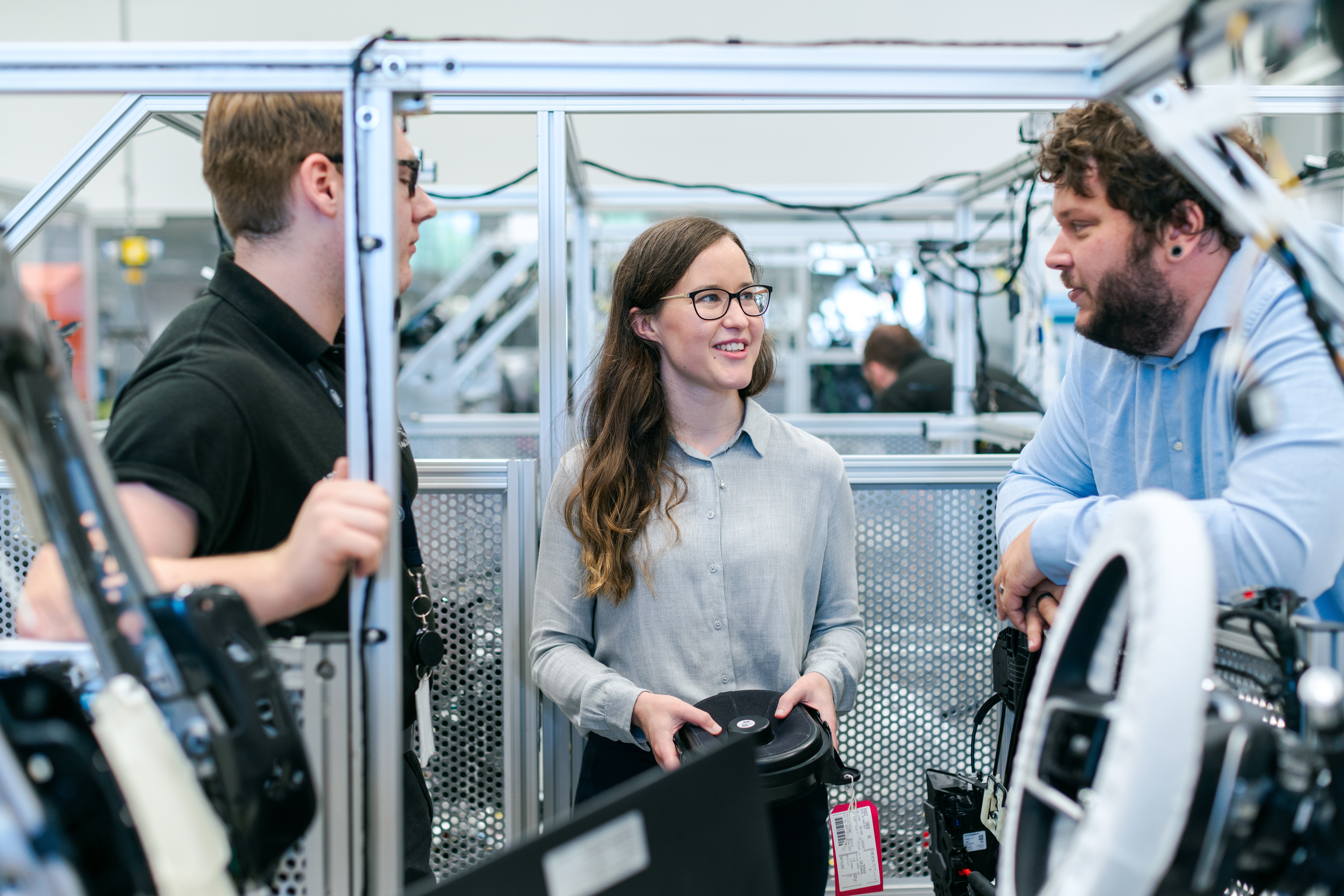
Three people talking in a factory. | Pexels/ ThisIsEngineering
The CEO was satisfied that the $10 million he spent fixing the problem and maintaining a good relationship with his stakeholders were worth it.
He often went down to the production line to see how the scale worked to ensure it was money well spent and it was still doing the proper job.
A few weeks later, the engineers reported that the number of boxes the scale was signaling had come down to zero and that there weren't any empty boxes being sent out.
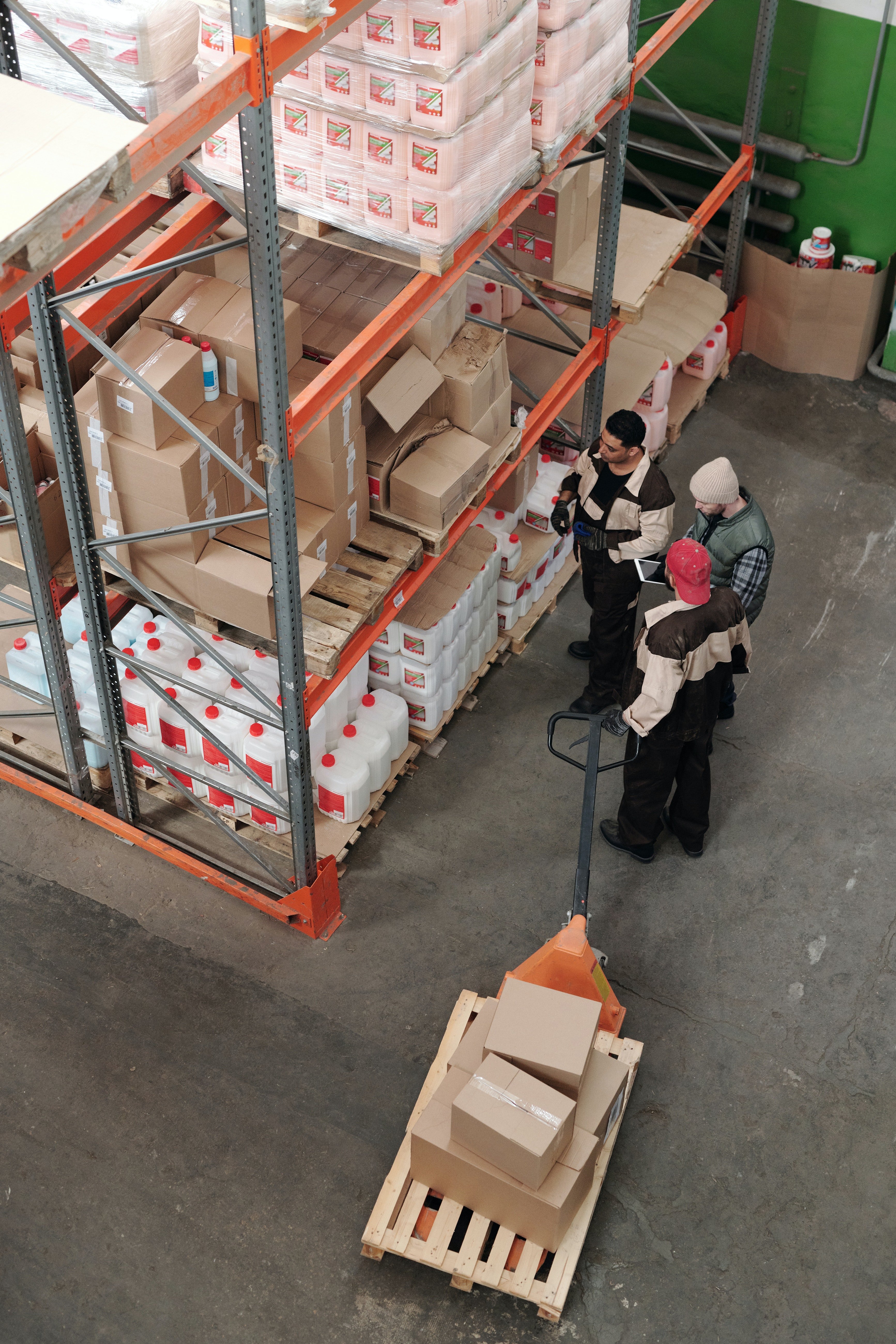
Three man standing next to a forklift. | Pexels/ Tiger Lily
Puzzled by this strange occurrence, the CEO marched down to the production line to inspect the scale and found that it was still in perfect working condition but that a fan was blowing on the boxes resulting in the empty ones flying into a nearby bin.
Flabbergasted, the CEO turned to ask one of the workers what was going on and why there was a $10 fan standing in front of his expensive system, and she replied:
"John, the kid from maintenance, put a fan there because he was tired of walking over, removing the box, and re-starting the line every time the bell rang."